Conductivity measurement saves refinery USD 100k per annum
A major Asian refinery with crude capacity close to 10 mt approached Stanhope-Seta to assess their options for automatic dosing of Static Dissipater Additive (SDA) in the Jet fuel stream.
Problems
The refinery was originally using an offline manual sampling procedure, testing the fuel at a certain number of points in the pipeline. The overall sampling and measurement procedure required to take multiple samples took in excess of eight minutes meaning rapid sampling was not possible. Typically three to four samples were drawn, taking over thirty minutes in total.
During the measurement procedure it was observed that conductivity readings decreased in value throughout the test. The decrease in conductivity value during the measurement phase was attributed to fuel polarisation.
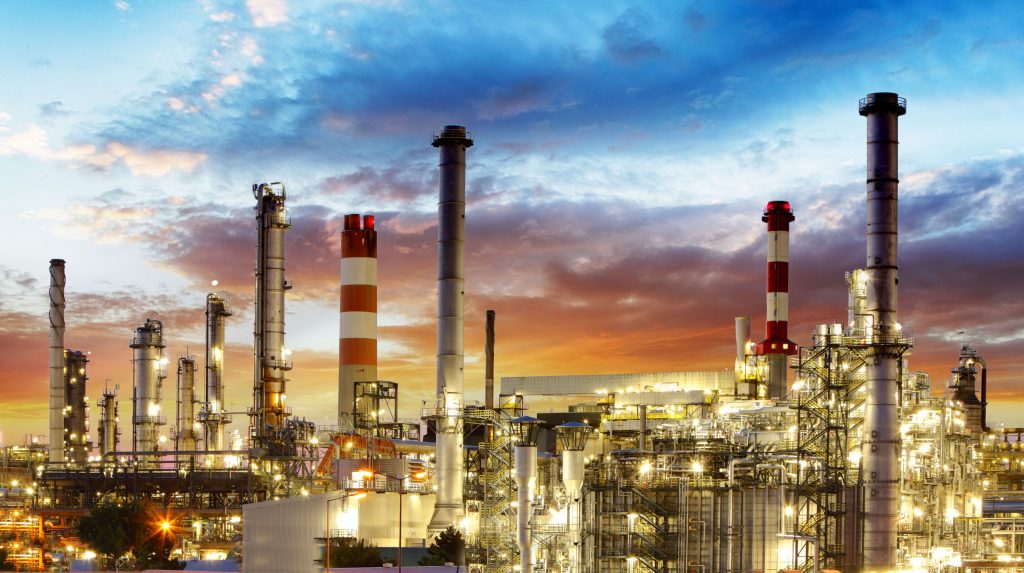
Using Stanhope-Seta’s Handheld Conductivity Sensor meant measurements could now be taken immediately, without the two minute delay while operators wait for the sample to dissipate any static charge.
The Handheld Conductivity Sensor works on AC measurement technology so any charges, or polarisation of the fuel do not affect the conductivity readings. The AC measurement technology also resolves the issues associated with reduced readings over time. Overall the sampling time halved from thirty minutes to fifteen minutes and the problem of inconsistent results resolved.
The Handheld Conductivity Sensor stored the data and sent it directly to the LIMS system via a PC interface for easy recall so no manual documentation was required, resulting in labour savings of over 100 hours annually.
Visit the 99708-0 Handheld Conductivity Sensor product page
With measurement consistency provided by the handheld conductivity meter it was immediately discovered that the manual SDA dosing system was providing inaccurate additive delivery, resulting in unnecessary increase of production costs due to fuel off specification.
The system records the conductivity and temperature via the current loop and a real time display enables data to be read directly.
As well as better control, the In-line Conductivity Sensor provided an estimated saving on SDA of USD 20,000 within the first three months. Capital cost recovery was expected within a six month period simply based on reduced SDA additive costs with additional savings being made on labour costs from less hand sampling.
Achieving better operational results the refinery also recognised that the In-line Conductivity Sensor raised the quality level of the produced fuel eliminating the high cost and associated liability of out of specification fuel leaving the facility.
Visit the 99500-0 In-line Conductivity Sensor product page
Download Conductivity Sensor Case Study PDF