Measuring the vapour pressure of crude oil gives an understanding as to which conditions cause bubbles to build up, helping to prevent costly damage to pipelines or vessels during transport or storage.
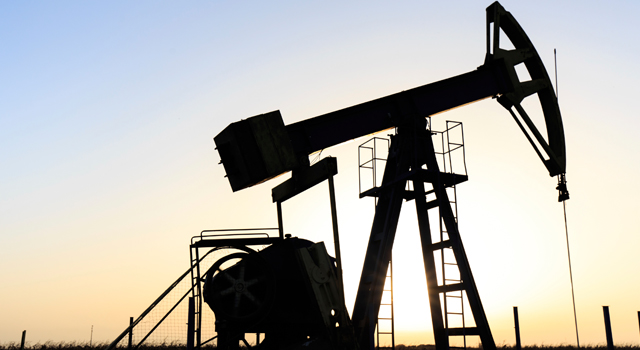
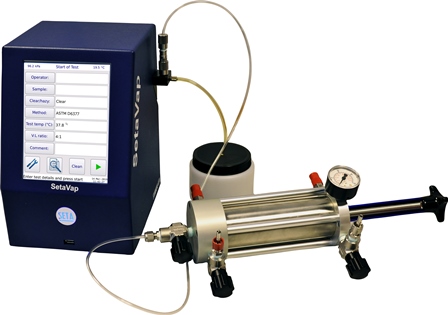
Measuring vapour pressure of crude oil
Stanhope-Seta’s Manual Piston Cylinder (80615-0), enables crude oil to be safely sampled and transported in full compliance to ASTM D6377 and ASTM D8009. An Inlet Connection Kit (80605-0) allows quick and easy set up.
Live crude oil contains a high amount of volatiles, so should be sampled and transported in a Floating Piston Cylinder (FPC) or Manual Piston Cylinder (MPC). A piston cylinder enables a sample to remain a liquid and be attached to the apparatus for testing without loss of volatile light ends. If a sample was taken in an open sampling vessel, such as a glass bottle, significant loss of light ends would occur, lowering the vapour pressure and giving an incorrect measurement. A sample within a glass bottle with the lid on represents a hazard if the temperature goes up, risking cracking glass, leakage or explosion.
The risks of high vapour pressure in crude oil
When extracted, crude oil is regarded as ‘live’ and could contain gases such as methane, ethane, propane and butane. These gases increase the vapour pressure of the crude. When the live crude oil is contained and transported in a pipeline or vessel, it is exposed to direct sunlight and heats up, this significantly increases the vapour pressure, which can cause the transportation medium to leak or worse to fracture. This, coupled with high flammability may lead to a very dangerous situation.
Therefore, the vapour pressure of crude oil is a key parameter when planning the transportation of crudes through different climate zones, helping to:
- Indicate how crude oil will perform during handling
- Give guidance on how transportation facilities should be built
View SetaVap4 Automatic Vapour Pressure Analyser for crude oil vapour pressure testing>